Packaging Machine Repair Service: Ensuring Marginal Downtime and Maximum Efficiency
Packaging Machine Repair Service: Ensuring Marginal Downtime and Maximum Efficiency
Blog Article
Ideal Practices for Making Certain Longevity and Dependability Through Product Packaging Equipment Fixing Solutions
In the competitive landscape of product packaging operations, making sure the durability and dependability of equipment is critical. Embracing finest methods in repair service services is critical, starting with the selection of certified service technicians that have the needed experience. Establishing a robust routine assessment and maintenance program can considerably alleviate unexpected break downs. By incorporating sophisticated tracking technologies and promoting tactical partnerships with repair work company, services can improve operational performance. Nonetheless, the efficiency of these techniques pivots on recognizing several key elements that can influence their implementation.
Significance of Normal Upkeep
The effectiveness of a packaging machine counts greatly on routine maintenance, which functions as a critical element in making certain optimal efficiency. This proactive technique not only boosts the device's long life yet additionally minimizes the threat of unforeseen break downs that can interrupt manufacturing routines. Routine upkeep consists of an organized evaluation of crucial elements, lubrication of relocating parts, and prompt substitute of damaged components.
Moreover, normal maintenance promotes a society of responsibility among team, as they come to be more knowledgeable about the devices and its needs. This understanding can result in quicker identification of anomalies, making certain that any type of irregularities are addressed promptly. Eventually, prioritizing normal maintenance is important for protecting the integrity, efficiency, and general performance of packaging machines in any production atmosphere.
Performing Regular Inspections
Conducting routine evaluations is an essential method in preserving the operational efficiency of product packaging machines. These assessments function as a positive action to recognize prospective problems before they escalate into costly breakdowns or operational hold-ups. By systematically examining vital parts, such as belts, motors, sensing units, and control systems, drivers can ensure that all equipment operates within optimum specifications.
Regular inspections need to be arranged based on the maker's recommendations and the certain use patterns of the devices. During these assessments, it is necessary to examine for deterioration, misalignments, and any kind of indicators of leakage or uncommon noises. Documenting the searchings for not only help in prompt repair work yet additionally assists establish a historic record that can notify future maintenance methods.
Moreover, routine examinations promote compliance with security requirements, making sure that the equipment operates within lawful and governing structures. This diligence not only safeguards staff members but likewise boosts general efficiency by decreasing unexpected downtime. Spending time and resources in carrying out thorough inspections eventually adds to the longevity and integrity of product packaging devices, reinforcing the relevance of this best practice in any operational setup.
Finding Qualified Repair Solutions
When selecting repair service services for product packaging devices, it is vital to focus on credentials and know-how. The performance and reliability of your product packaging procedures depend considerably on the ability degree of the professionals you engage. Begin by examining the provider's certifications, guaranteeing they have relevant sector certifications that demonstrate their expertise and competency in packaging machinery.
Following, consider the service provider's experience in the particular sort of equipment you operate. A repair work service with a tried and tested track record in your equipment brand name and design will likely recognize the nuances included and can provide a lot more effective solutions - packaging machine repair service. Additionally, ask concerning the training and continuous education and learning of their specialists, as the packaging sector constantly evolves with new technologies
Customer responses is one more crucial aspect; choose reviews or reviews from previous customers. This will certainly provide insights into the service high quality and reliability of the repair work service provider. Finally, review the response time and support choices readily available, as prompt service can reduce downtime and preserve performance. By meticulously picking certified repair services, you can guarantee your packaging equipments operate at optimal efficiency, ultimately protecting your investment and improving general efficiency.
Executing Preventative Methods
Proactive maintenance is important for taking full advantage of the life-span and efficiency of packaging machines. Implementing preventative approaches can substantially lower the possibility of unexpected breakdowns and costly repairs. An extensive upkeep schedule need to be established, describing regular inspections, cleaning, and component substitute based upon the supplier's referrals and functional needs.
Moreover, training staff on the proper original site procedure and handling of equipment is critical. Workers should be educated on identifying prospective problems early, such as uncommon noises or irregular efficiency, which might indicate underlying issues. This not only boosts security yet also cultivates a culture of accountability and diligence.
One more reliable preventative approach is the usage of problem surveillance innovations. These tools can offer real-time data on maker performance, permitting drivers to spot anomalies before they intensify. Implementing a systematic method to lubrication and making sure that all moving parts are appropriately kept will better boost functional integrity.
Monitoring Performance Metrics
How can companies efficiently monitor the efficiency of their product packaging machines to guarantee optimal performance? Tracking performance metrics is essential for recognizing locations of renovation and preserving high operational standards. Organizations should apply a thorough efficiency surveillance system that records key information factors such as maker uptime, manufacturing speed, and mistake prices.
Using real-time information analytics devices can assist in the continuous analysis of these metrics. By analyzing fads over time, organizations can identify persisting problems, causing more enlightened choices pertaining to maintenance and repair work - packaging machine repair service. Consistently scheduled evaluations need to additionally be carried out to compare real performance versus developed criteria
Additionally, incorporating predictive maintenance approaches based on efficiency metrics can assist alleviate unanticipated downtime. By anticipating possible failings, companies can arrange repair work during non-peak hours, consequently reducing interruptions to production.
Educating personnel to use and understand efficiency metrics is just as essential - packaging machine repair service. Encouraged workers can add beneficial insights into functional inefficiencies and recommend enhancements
Verdict
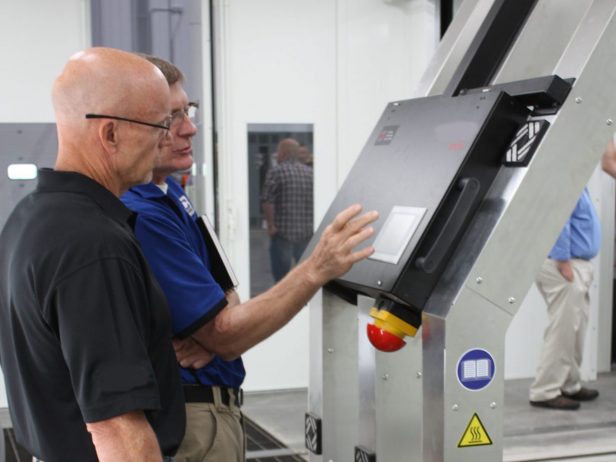
The efficiency of a packaging maker counts heavily on routine maintenance, which serves as a critical component in guaranteeing optimal performance.When choosing fixing solutions for packaging makers, it is essential to focus on credentials and competence. By thoroughly choosing qualified repair services, you can guarantee your product packaging makers operate at ideal performance, inevitably guarding your investment and boosting general efficiency.
Just how can companies properly keep track of the efficiency of their product packaging makers to make sure ideal performance?In final thought, the longevity and reliability of product packaging makers hinge on the execution of ideal methods in repair solutions.
Report this page